Forty Mile Fiber Ring
Forty miles is 211,000 feet. This is the distance over which we installed a ring of fiber optic cable. The purpose was to link two data centers for increased bandwidth, speed and reliability. 65% of the work was underground. The remaining 35% was aerial fiber. Placed to avoid significant obstacles. Fiber Optic cable placement splicing and testing will become increasingly important as the hunger for bandwidth and performance grows. Electric Conduit Construction takes pride in its ability to carry out this type of work with high quality results and safe work habits.
Much of the underground work on this project required Horizontal Directional Drilling. Some of the drill shots were 1,500 to 2,000 feet long. This work required careful planning, permitting and execution. Directional drilling is more than pointing the drill bit in the right direction and guiding it to the exit point. Our crews follow a strict Utility Damage Prevention Plan that forms the backbone of our policies and procedures to avoid cross bores or any type of utility hit. When fiber is placed in underground urban areas there will be utility conflicts. Each conflict has to be resolved through positive location and identification. There are times when even this is not good enough and we rely on our experienced foremen to spot potential conflicts and perform exploratory pot-holing to check for unmarked utilities.
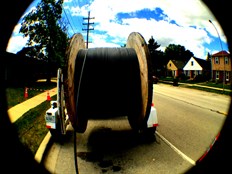
Fiber Spool
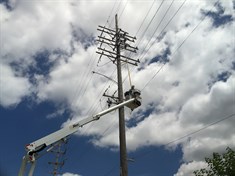
Power company opens circuit
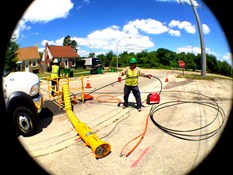
Coiling excess fiber
The portion of this route that utilized existing open conduit runs had to be rodded and cleared first. Then new conduit and inner duct was pulled through. Many of the existing manholes were completely flooded and each had to be pumped down and maintained until the new conduit was in place. All of the conduit splices utilized specialized fittings with O-ring seals to create a watertight connections. Confined space entry into manholes containing underground power is not for the faint of heart. Strict safety procedures guide the foremen and crew through the pump down phase, atmospheric sampling inside the space, and thermal imaging of the power cables.
Much of the aerial fiber followed the route of 135kv transmission lines. The safety requirements on the project were very high. Power had to be interrupted on several occasions due to the proximity of the self-supporting fiber to high voltage lines. All work was done carefully and meticulously. While placing fiber optic cable is not glamourous it can be very dangerous.
When the conduit work was complete the fiber crews came in with 25,000 foot spools of self-supporting fiber. The decision was made to use self-supporting fiber because of the high percentage of aerial runs. It was easier to run the self-supporting fiber through underground conduit in order to minimize cutting, splicing and testing in the transition areas between aerial and underground.
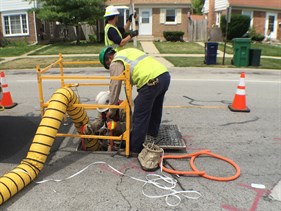
Preparing to enter a manhole
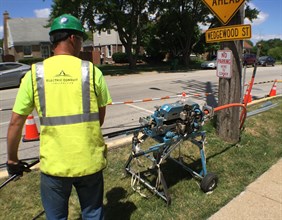
Blowing fiber
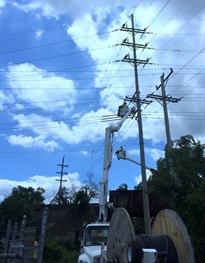
Transmission lines
Crews worked long hours to complete the project in the four month time period allotted to them. Challenges included, ground water control in manholes, confined space entry and monitoring, directional drilling and maintaining the accuracy of the drill profile, working near high voltage power lines, and traffic control.
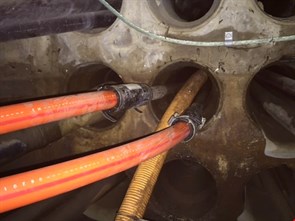
New fiber in existing ducts
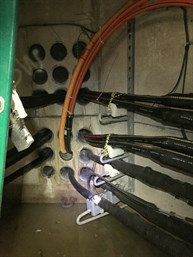
Note watertight connections
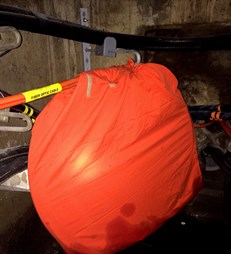
Excess fiber coiled inside fire bag
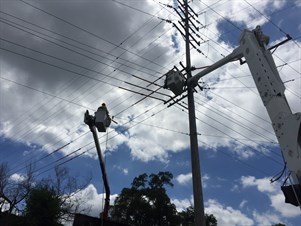
Aerial fiber placement
Project Facts:
- 211,000 feet of self-supporting fiber optic cable
- 137,000 feet underground
- 73,850 above ground
- Four month duration
Safety Facts:
-
Electrical 135 kv and 35 kv
-
Confined space
-
Traffic
-
Slips trips and fall hazards
-
PPE including hard hats, safety glasses, steel toed boots, hot boots and gloves, double layers of FR clothing
This project was completed safely and on time. We thank our project managers, superintendents, foremen and laborers for their hard work, great safety attitude and willingness to work hard to complete this project.
All photos by M. Purpura. Thanks to Ztylus for the 4:1 iPhoneography Kit that made these images.